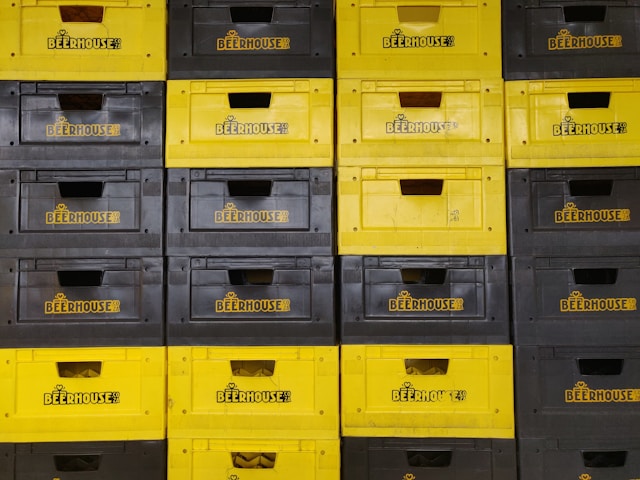
Key Takeaways:
- The remarkable growth of injection molding has made it a linchpin in manufacturing, contributing to various industry advancements.
- Technological innovation pushes the bounds of mold design, resulting in a manufacturing landscape where precision is paramount.
- Modern injection molding shapes a more efficient and responsible production ethos by balancing ecological considerations with economic demands.
Table of Contents:
- Introduction
- The Evolution of Injection Molding Methods
- Critical Components of High-Precision Injection Molds
- Injection Molding Techniques for Optimal Performance
- Reducing Waste and Enhancing Efficiency in Mold Sampling
- Quality Control and Testing in Injection Molding
- Advanced Materials in Injection Molding
- The Role of Software in Modern Injection Molding
- The Future of Injection Molding Technology
- The Impact of Precision Molding on Different Industries
- Conclusion
Once seen as the future of manufacturing, injection molding has firmly established itself as the standard for creating diverse and intricate plastic products. This process encompasses significantly more than simply melting plastic and shaping it into form; it’s about achieving exactness in dimensions, strength in product structure, and production efficiency. With industries ranging from medical devices to automotive parts relying on this technology, refining injection molding techniques has only gained momentum, consistently pushing the boundaries of what can be created.
The Evolution of Injection Molding Methods
The inception of injection molding can be traced back to the late 19th century, and since then, it has experienced a substantial transformation. Initially used to mass-produce simple items such as buttons and combs, injection molding has evolved, culminating in complex parts with astonishing precision. The contribution of cutting-edge machinery, evolved molding materials, and refined practices has been immense. Each stage in this chronological progression has been marked by innovation, such as the introduction of thermoplastic materials, which opened up new horizons in manufacturing capabilities.
Critical Components of High-Precision Injection Molds
Every high-precision mold owes its success to its core elements – the engineering design, choice of materials, and the fine-tuning of mold parameters. The engineering design is a complex task that can now harness advanced computational tools to predict mold behavior under various conditions. Material choice has expanded beyond traditional metals, incorporating alloys and composites with superior durability and machining possibilities. These materials ensure the molds retain their precision even after numerous cycles, producing consistent and high-quality parts. The balancing act between design complexity and material resilience sets high-precision molds apart.
Injection Molding Techniques for Optimal Performance
Selecting the proper technique for injection molding can have a profound impact on the performance of the final product. Techniques differ based on the requirements of the end product, and parameters such as temperature, pressure, and injection rate must be meticulously calibrated. Robotic precision has been introduced to uphold meticulous standards throughout production runs, ensuring that every unit produced matches the prototype’s specifications. The interplay between operator expertise and robotic precision leads to an era where error margins are approaching zero.
Reducing Waste and Enhancing Efficiency in Mold Sampling
Minimizing waste in the manufacturing process is not just beneficial for the environment; it is also economically advantageous. Mold sampling efficiency leads to better resource use and less material waste. To produce more with less, companies emphasize lean manufacturing principles, which are now rigorously applied in injection molding. Pioneering research has contributed significantly to this area, as seen in studies that integrate novel strategies to minimize defects and streamline material usage, resulting in more sustainable practices.
Quality Control and Testing in Injection Molding
Ensuring each component conforms to quality standards is central to maintaining trust in manufactured products. Injection molding is no exception, and it utilizes an array of quality control and testing methodologies to preserve production integrity. Challenges such as managing shrinkage, warping, and other potential defects are met with a robust quality control regimen. Tests range from visual inspection to dimensional measurements, functional testing, and destructive testing where necessary. This thorough approach is essential for industries where precision is not a luxury but a requirement.
Advanced Materials in Injection Molding
The materials science landscape is burgeoning, and with it, the types of materials available for injection molding. Innovations in this realm are opening pathways to creating strong, light, and sustainable products. Introducing biomaterials and integrating nanocomposites exemplify how material innovation drives product performance and ecological responsibility. Material scientists and engineers collaborate to test the limits of these new materials, ensuring they rise to the demanding expectations of modern consumers and regulators alike.
The Role of Software in Modern Injection Molding
Software’s potential in refining injection molding can’t be overstated. Everything from mold design to the molding process simulation can now be rendered with incredible precision thanks to sophisticated CAD and computer-aided engineering (CAE) software. These tools predict the behavior of materials under various conditions, allowing for adjustments before actual production and saving time and resources. Additionally, they function as collaborative platforms, enabling designers and engineers to hone their crafts and develop methods realized only with digital precision.
The Future of Injection Molding Technology
The trajectory of injection molding is toward greater integration with emerging technologies. Aspects of Industry 4.0, including the Internet of Things and Big Data analytics, are being eyed as crucial elements in the future molding factory. There is significant anticipation surrounding the alignment of 3D printing with injection molding, representing a leap forward in custom fabrication, potentially altering production lines by reducing the need for traditional tooling and offering unparalleled design flexibility.
The Impact of Precision Molding on Different Industries
From the minutiae of medical components to the expansive dashboards of automobiles, precision molding continues to serve as the backbone of an array of industries. Each sector presents unique challenges, demanding custom solutions that injection mold technology strives to provide. Striking the right balance between precision, strength, and aesthetically pleasing design is an ongoing challenge eagerly accepted by the molding industry. The advancements in this field consistently push the envelope, ensuring that future products will continue exceeding our performance and innovation expectations.
Conclusion
Injection molding epitomizes the convergence of art and science. As we’ve outlined, the myriad of aspects that contribute to the precision and efficiency of this technique are each crucial in their own right. The culmination of these fine-tuned elements streamlines the production process and ensures each part meets exacting standards. Looking at the horizon, it’s evident that the significance of injection molding will only grow. For ongoing insights into this vast and dynamic field, staying informed through credible sources such as PlasticsToday and updates on the role of precision in industries like medtech, as highlighted by ManufacturingTomorrow, is invaluable. They provide not just news but thoughtful analysis and projections for an industry that shapes our daily lives in countless ways.
More Stories
Understanding the Importance of Regular Electrical Maintenance in Homes
The Evolution and Impact of Graphic Design in Business Communications
Ways Machine Vision Integration Can Revolutionize Manufacturing